The difference between conductor shielding and insulation shielding
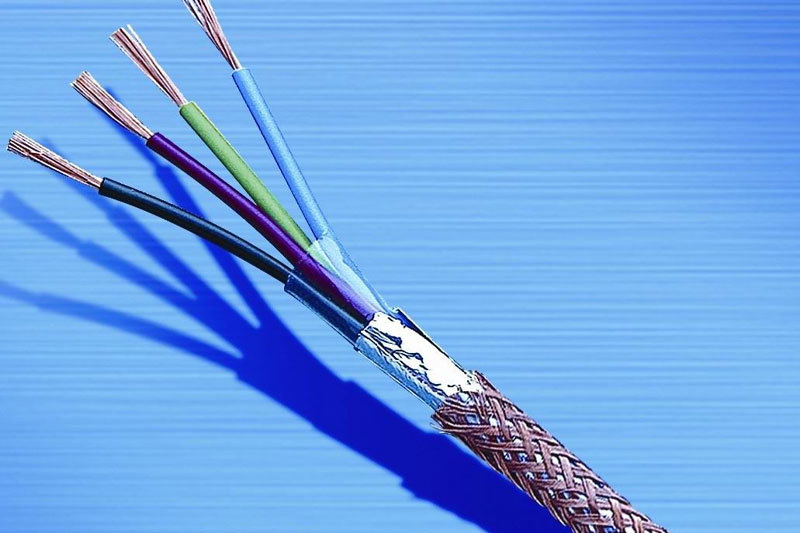
The conductor shield is used between the conductor and the insulating material. The insulating shield is extruded on the surface of the insulating material and interacts with the coaxial natural or synthetic tape and sheath (if any). Shielding materials are essentially semi-conductive materials because they act as a stress transition between the insulation and the conductor in order to obtain a free charge system. The semi-conductive materials used as conductor shields and insulation shields are similar, but their physical and chemical properties will be different. Therefore, the insulation shield must be strippable (in order to easily peel off the insulation shield when installing the cable joint or terminal). The conductor shield is the opposite; it must adhere firmly to the insulating surface (to prevent interfacial microporosity and moisture penetration). The modulus and tear strength of the insulation shield are important parameters, as is its adhesion strength, which is determined by the nature of the copolymer, the type of additives and the processing technology.
According to the relevant industry standards, cables with rated voltages exceeding 2kV require conductor shielding.
For extruded insulated cables, the conductor shielding layer is extruded on the conductor as a semi-conductive layer and insulation at the same time, becoming a stress relief layer. The reason why it is important to keep the interface between the conductor shield and the insulating layer free of pores or impurities is that the electric field strength in this area is the highest in the cable.
The conductor shield and the insulation are crosslinked at the same time during extrusion, so that a strong bond can be formed, and the formation of micropores at the critical interface can be minimized.
In view of compatibility, the conductor shielding material is often the same as or similar to the insulating material. Special carbon black is added to the conductor shield to ensure a certain conductivity. The cable industry standard requires that the resistivity of the conductor shielding material should not exceed 1000 Ω · m. These standards also require electrical materials to pass a long-term resistance stability test at emergency operating temperatures to ensure the conductivity of the conductor shield and the long-term life of the cable.
The characteristics and compatibility requirements of the insulation shield are similar to those of the conductor shield. However, the standard requirement for the volume resistivity of the insulation shield is not greater than 500 Ω · m. Compared with the conductor shield, the reduction of the required value of resistivity means that the outer metal shield may not continuously contact the insulation shield (such as a gap between the shield wires), and in fact, when the cable is live, personnel may contact the outer layer of the cable.
The non-metallic screen layer is directly squeezed on the insulation, and the electric field strength on the interface is lower than the field strength of the conductor shield and the insulation layer section. For the convenience of installing joints and terminals, the insulation shield does not need to be bonded with the insulation layer when the voltage is not higher than 46kV. At higher voltages, it is strongly recommended to use a shield with bonded insulation.
Key words:
Share