XLPE cable shield material characteristics?
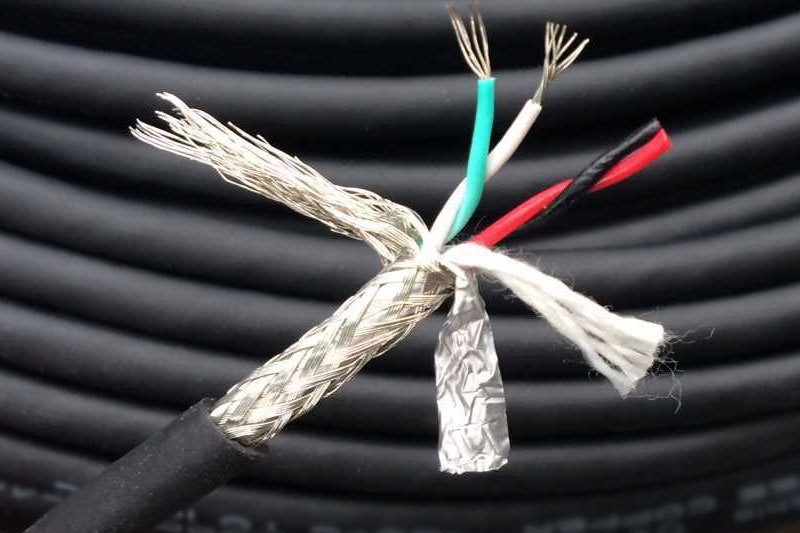
The so-called "shielding" on the cable structure is essentially a measure to improve the electric field distribution. The cable conductor is formed by stranding a plurality of guide wires, it is easy to form an air gap between the insulation layer, and the surface of the conductor is not smooth, which will cause electric field concentration. A shielding layer of semi-conductive material is added to the surface of the conductor, which is equipotential with the shielded conductor and is in good contact with the insulating layer, thereby avoiding partial discharge between the conductor and the insulating layer. This layer of shielding, also known as the inner shield.
At the contact between the insulation surface and the sheath, there may also be gaps. When the cable is bent, the insulation surface of the oil-paper cable is easy to cause cracks. These are all factors that cause partial discharge. A shielding layer of semi-conductive material is added on the surface of the insulating layer, which has good contact with the shielded insulating layer and is equipotential with the metal sheath, thereby avoiding partial discharge between the insulating layer and the sheath.
The material of the shielding layer is a semi-conductive material having a volume resistivity of 10 ^ 3-10 ^ 6 Ω · m.
The shield material of the extruded insulated cable is a polymer with carbon black particles.
For extruded insulated cables without metal sheaths, in addition to the semi-conductive shielding layer, a metal shielding layer wrapped with copper tape or copper wire should be added. The function of this metal shielding layer is to pass the capacitive current during normal operation; when the system is short-circuited, it serves as a short-circuit current channel and also plays a role in shielding the electric field. In the design of cable structure, according to the size of the system short-circuit current, the cross-sectional area of the metal shielding layer is required.
Characteristics of XLPE Cable Shielding Materials
Polymers used as cable shielding materials are vinyl copolymer materials. They are polymers of propylene and other monomers such as EVA, EEA, EBA, etc. Essentially, they are elastomeric materials. Each co-monomer provides different properties to the co-polymer material used for shielding. As with insulating materials, there are concerns about molecular weight and molecular weight distribution, as well as extrusion characteristics. As with the cross-linking type insulating material, the shielding material also needs to be able to be cross-linked; however, crystallinity is not a big problem, and carbon black is currently the most commonly used, which affects the processing and performance of the material.
What is the role of carbon black? The semi-conductive carbon black can be added to the copolymer material to obtain semi-conductive. After addition of carbon black and appropriate treatment, the carbon black filled polymer is semiconductive. Carbon black is also called furnace black or acetylene black; furnace black can be obtained by incomplete oxidation of petroleum and natural gas, and acetylene black is a decomposition product of acetylene at high temperature. In addition to being electrically conductive, carbon black is required to have a smooth surface, appropriate particle size, purity, and dispersibility in the polymer.
It has long been recognized that the properties of elastomers with carbon black additions are governed by many factors: ① the nature of the carbon black, ② the concentration of the carbon black, ③ the nature of the polymer matrix, ④ the crosslinking system. The latter is not the current task, but other factors are interrelated.
When the carbon black forms aggregates in the polymer, conductivity is obtained, which allows electrons to flow. It will be appreciated, however, that electron tunneling between the aggregates causes conductive behavior in the semiconducting layer. The final electrical properties of the semi-conductive shielding material are determined by the aggregate structure and the size of the carbon black. Figure 5-17 reveals how the interrelationships affect physical and electrical properties.
Carbon blacks with a high quality structure tend to impart greater conductivity and a hard structure to aggregate to form clusters. When carbon black is added to the elastomer, this structure will be destroyed, and the degree of damage is affected by the type of carbon black and the mixing process. Therefore, reasonable control is critical. The concentration of carbon black in the semi-conductive shielding material depends on the type of carbon black and ranges from 12% to 30%.
A smooth surface is essential to ensure that there are no protrusions at the junction with the insulation; protrusions can lead to the formation of high stress points, and water trees can easily form in wet environments. When present at the semi-conductive shield interface, the protrusion depends on the geometry and height of the carbon black. Therefore, the dispersibility and fineness of carbon black are the key factors to obtain a uniform and smooth surface. Uniform dispersion of the carbon black in the polymer, as well as proper mixing and processing techniques, are necessary.
Purity is another key factor. When prepared, the carbon black may contain small amounts of moisture, sulfur, and inorganic salts. Sulfur impairs electrical properties, and most of the inorganic salts come from water used for cooling during processing. Much attention has been paid to inorganic ions in the past. Compared with acetylene black, furnace black used until the mid-1980s has more ion content; this will lead to the formation of water trees, and thus failure. Recently, furnace black with increased cleanliness has begun to be used; it should be noted that older cables use furnace black in their shielding materials.
Other additives may also be added. For example, other additives are added to obtain an insulation shielding material having a certain stripping property, but such additives are not allowed to be added to the conductor shielding material. The conductor shielding material cannot be stripped.
Finally, shielding materials containing carbon black also need to have extrudability and crosslinkability, just like insulating materials. In this case, a three-layer extrusion can be obtained within the scope of the design. The factors that affect the conductivity are the type and content of carbon black, processing technology, crosslinking system and other components. The type of base polymer is important; for example, for conductor shielding, the combinations are as follows:(a) furnace black copolymerized with EVA, EEA, (B) acetylene black copolymerized with EVA, EBA.
Key words:
Share